Hello! Want to know more about heat treatment? We have the best explanation here, welcome to browse, have feedback can give us feedback, thank you for your cooperation! !
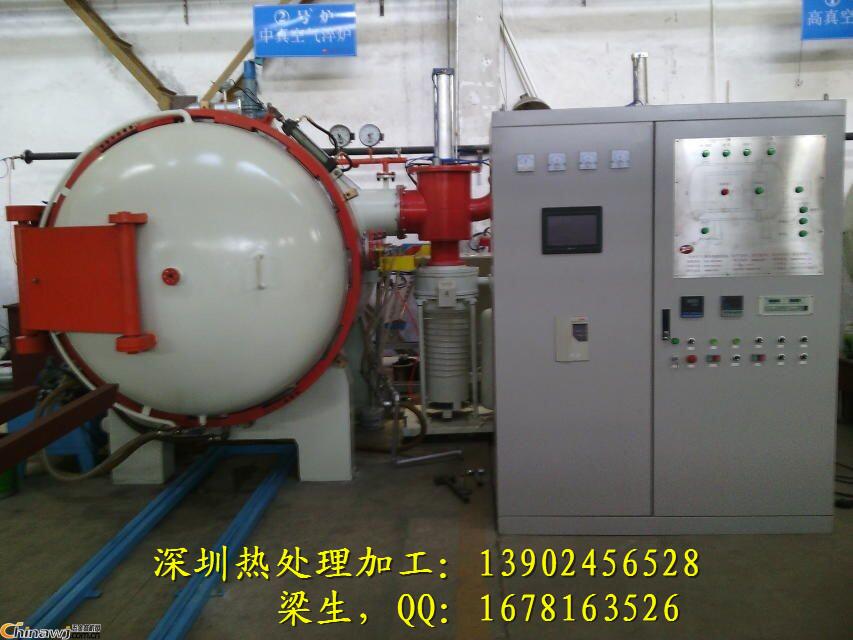
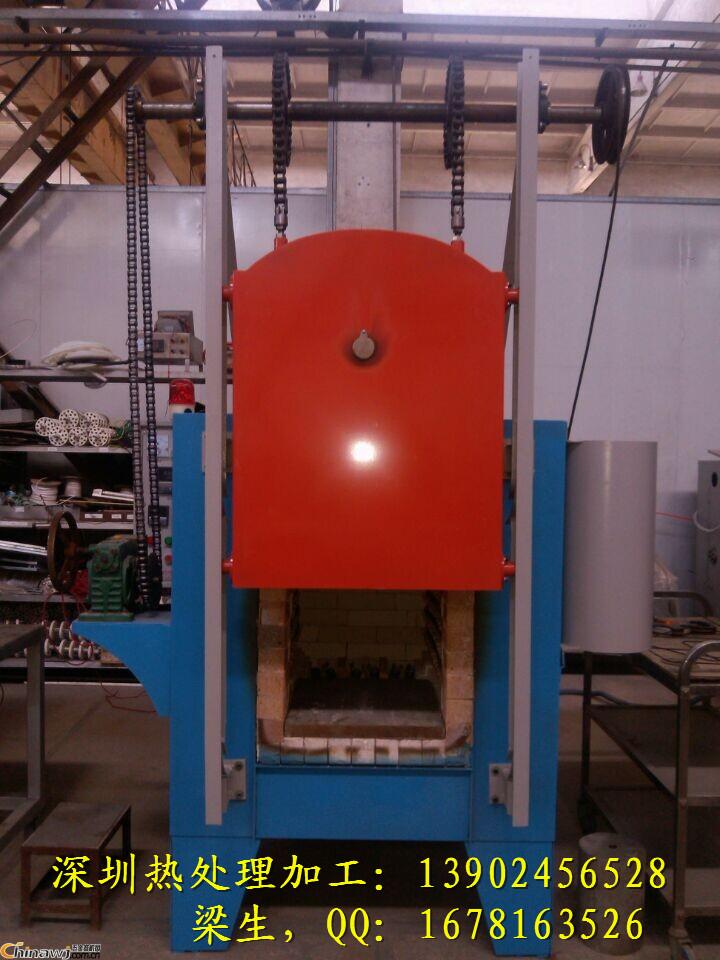
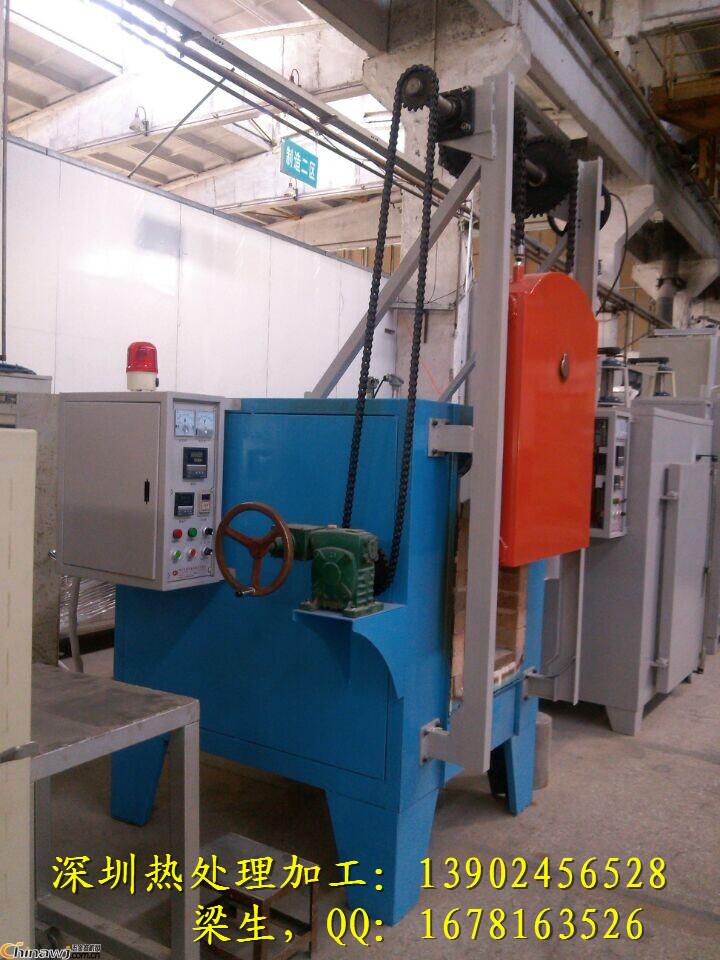
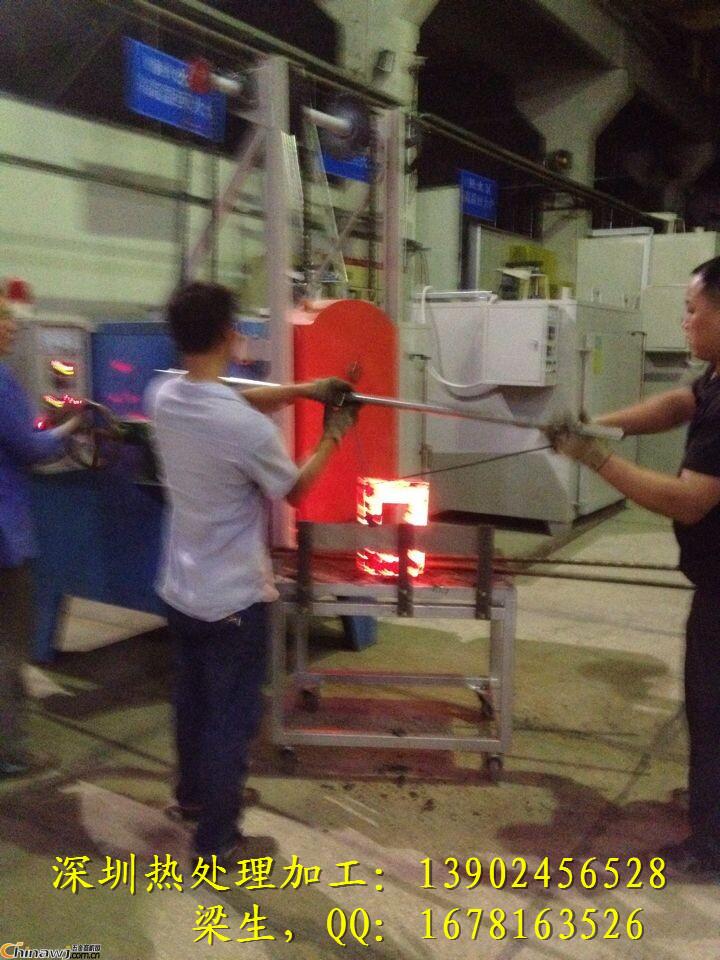
Heat treatment knowledge
Hello! Want to know more about heat treatment? We have the best explanation here, welcome to browse, have feedback can give us feedback, thank you for your cooperation! !
Surface heat treatment
1 Surface quenching Surface quenching is a method of partial quenching in which the surface layer of steel is hardened to a certain depth while the core portion remains unquenched. When the surface is quenched, the surface of the rigid part is quickly heated to a quenching temperature by rapid heating. When the heat is too late to pass through the core of the workpiece, it is immediately cooled to achieve local quenching.
The purpose of surface quenching is to obtain a surface with high hardness and high wear resistance, while the core still maintains the original good toughness, and is often used for the spindle of machine tools, gears, and crankshafts of engines.
Surface quenching uses a variety of rapid heating methods, such as induction, flame, electrical contact, laser, etc. The most widely used is the induction heating method.
2 Surface quenching and tempering The metal heat treatment process of reheating the quenched workpiece to a suitable temperature lower than the lower critical temperature and cooling in air or water, oil and the like after a certain period of time. Or the quenched alloy workpiece is heated to a suitable temperature for a certain period of time and then slowly or rapidly cooled. Generally used to reduce or eliminate the internal stress in the hardened steel, or reduce its hardness and strength to improve its ductility or toughness.
3 Physical Vapor Deposition (PVD) technology means that under vacuum conditions, the material source - solid or liquid surface is vaporized into gaseous atoms, molecules or partially ionized into ions, and passed through low pressure gas. (or plasma) process, a technique of depositing a film having a specific function on the surface of a substrate. The main methods of physical vapor deposition include vacuum evaporation, sputtering coating, arc plasma plating, ion plating, and molecular beam epitaxy. Up to now, physical vapor deposition technology can not only deposit metal films, alloy films, but also compounds, ceramics, semiconductors, polymer films, and the like.
4 Chemical vapor deposition (CVD) Chemical vapor deposition (CVD) is a process in which a reaction substance is chemically reacted under gaseous conditions to form a solid material deposited on the surface of a heated solid substrate to produce a solid material. It essentially belongs to the gaseous mass transfer process of the atomic category. In contrast, physical vapor deposition (PVD).
Overall heat treatment
1 Annealing Annealing is a metal heat treatment process that involves slowly heating a metal to a temperature for a sufficient period of time before cooling at a suitable rate. The purpose is to reduce hardness, improve machinability, eliminate residual stress, stabilize size, reduce deformation and crack tendency, refine grains, adjust microstructure, and eliminate tissue defects.
2 Normalizing Normalizing, also known as normalizing, is to heat the workpiece to Ac3 or Acm above 40~60 °C. After holding for a period of time, remove the metal heat treatment process from the furnace in the air or spray water, spray or blow air. The purpose is to make the grain refinement and the carbide distribution uniform, remove the internal stress of the material, and reduce the hardness of the material.
3 Quenching of quenched steel is to heat the steel to a temperature above the critical temperature Ac3 (hypoeutectoid steel) or Ac1 (hyper-eutectoid steel), keep it for a period of time, make all or part of austenite, and then cool it by more than critical The speed of the cold is rapidly cooled to below the Ms (or isothermal near Ms) for a martensite (or bainite) transformation heat treatment process. The solution treatment of materials such as aluminum alloys, copper alloys, titanium alloys, tempered glass, or heat treatment processes with rapid cooling processes is also referred to as quenching.
4 Quenching and tempering The metal heat treatment process of reheating the quenched workpiece to a suitable temperature lower than the lower critical temperature and cooling in a medium such as air or water or oil after a certain period of time. Or the quenched alloy workpiece is heated to a suitable temperature for a certain period of time and then slowly or rapidly cooled. Generally used to reduce or eliminate the internal stress in the hardened steel, or reduce its hardness and strength to improve its ductility or toughness.
5 high temperature tempering High temperature tempering is to quench the parts, then heat to 500 ~ 650 ° C, usually heated to a certain temperature of the psk line (critical point Ac1), after a period of insulation, cooling at an appropriate speed. [1]. High temperature tempering gives a mixture of ferrite + fine-grained cementite, ie, tempered sorbite structure. It has excellent comprehensive mechanical properties and is used for tempering after quenching of structural parts, such as connecting rods, bolts, gears and shafts. Quenching + high temperature tempering is called quenching and tempering, which is generally used for subsequent treatment of quenching. Quenching + high temperature tempering is called quenching and tempering treatment, and has wide application in industrial production. The tempering temperature range is 500-650 degrees Celsius, which is beneficial to completely eliminate internal stress and improve the plasticity and toughness of the metal. The tempering is generally cooled in air. The hardness is generally between 25 and 35 HRC, and the structure after tempering is tempered sorbite. Mainly used in various types of connecting and transmission structural parts made of carbon steel and alloy steel with carbon content of 0.3%-0.5%.
6 quenching and tempering (quenching + high temperature tempering = quenching and tempering) Most of the materials work under the action of relatively large dynamic loads, they are subjected to stretching, compression, bending, torsion or shearing, and some surfaces also have friction. Requires a certain degree of wear resistance and so on. In short, the parts work under a variety of composite stresses. These parts are mainly structural parts of various machines and mechanisms, such as shafts, connecting rods, bolts, gears, etc., which are commonly used in the manufacturing industries such as machine tools, automobiles and tractors. Especially for large parts in heavy machine manufacturing, the quenching and tempering process is used more. Therefore, the quenching and tempering treatment occupies a very important position in the heat treatment.
The tempering parts in mechanical products are not exactly the same because of their different stress conditions. In general, all kinds of tempering parts should have excellent comprehensive mechanical properties, that is, appropriate combination of high strength and high toughness to ensure long-term smooth operation of parts.
7 Stabilization Any heat treatment process that stabilizes the structure and eliminates residual stress to keep the shape and size of the workpiece within the specified range.
8 Solution treatment The material or workpiece is heated to a suitable temperature and held for a sufficient time to fully dissolve the soluble phase, and then rapidly cooled to room temperature to obtain a heat treatment process for the supersaturated solid solution.
9 Water toughness treatment Water toughness treatment is actually a solution treatment, which is commonly used in high manganese steel. The as-cast microstructure of high manganese steel is composed of austenite, carbide and a small amount of phase change product pearlite. The carbide precipitated along the austenite grain boundary reduces the toughness of the steel. To eliminate the carbide, the steel is heated to the austenite temperature (1050-1100 ° C, depending on the fine or coarse carbide in the steel) and kept warm for a period of time. Time (1h per 25mm wall thickness), the carbides in the as-cast structure are basically solid solution into the austenite, and then rapidly cooled, resulting in a single subcooling
10 Aging treatment The aging treatment can be divided into natural aging and artificial aging. Natural aging is to place the casting in the open space for more than half a year, so that it slowly deforms, so that the residual stress is eliminated or reduced. Artificial aging is to heat the casting to 550 ~ 650 ° C for stress relief annealing, it saves time than natural aging, residual stress removal is more thorough, but the effect release is not complete compared to natural. “The two materials gain strength in different ways,†Menzemer said. “The 6061 aluminum alloy is obtained by heat treatment, sometimes called artificial aging. T6 is the optimum aging for maximum strength.
Chemical heat treatment
1 Carburizing Carburizing: It is a kind of metal surface treatment. Most of the carburizing is low carbon steel or low alloy steel. The specific method is to place the workpiece into an active carburizing medium and heat it to 900-950 degrees Celsius. The single-phase austenite region, after sufficient time of incubation, allows the activated carbon atoms decomposed in the carburizing medium to penetrate into the surface layer of the steel, thereby obtaining high carbon in the surface layer, and the core remains the original composition. Similar to low temperature nitriding treatment. This is a common heat treatment process for metal materials, which can achieve high hardness and improve the wear resistance of the surface of the carbonized workpiece.
2 Carbonitriding (oxidation) Carbonitriding of steel: Carbonitriding is a process of simultaneously infiltrating carbon and nitrogen into the surface of steel. Conventionally, carbonitriding is also called **. At present, the application of medium temperature gas carbonitriding and low temperature gas carbonitriding (ie gas nitrocarburizing) is widely used. The main purpose of carbon monoxide in medium temperature gas is to improve the hardness, wear resistance and fatigue strength of steel. The low temperature gas carbonitriding is mainly nitriding, and its main purpose is to improve the wear resistance and seizure resistance of steel.
3 Nitriding Nitriding is a chemical heat treatment process in which nitrogen atoms are infiltrated into the surface of a workpiece in a certain medium at a certain temperature. Common liquid nitriding, gas nitriding, ion nitriding. The traditional gas nitriding is to put the workpiece into a sealed container, and to pass the flowing ammonia gas and heat it. After a long time of heat preservation, the ammonia gas is thermally decomposed to generate active nitrogen atoms, which are continuously adsorbed to the surface of the workpiece and diffused into the surface layer of the workpiece. , thereby changing the chemical composition and structure of the surface layer to obtain excellent surface properties. If carbon is simultaneously infiltrated during the nitriding process to promote the diffusion of nitrogen, it is called nitrocarburizing. Commonly used are gas nitriding and ion nitriding, so that the steel after nitriding can obtain high surface hardness, wear resistance, fatigue strength, seizure resistance, resistance to atmospheric and superheated steam corrosion, and resistance to tempering and softening. And reduce the sensitivity of the gap.
4 Nitrocarburizing The chemical heat treatment process of nitriding mainly infiltrating carbon. Nitrocarburizing, which has been widely used in industrial production, has a gas method and a molten salt method.
5 seepage other non-metal
6 metal infiltration metal infiltration, English: diffusion metallizing, refers to the process of infiltration of metal atoms into the surface layer of steel. It is to alloy the surface layer of steel to make the surface of the workpiece have certain alloy steel and special steel characteristics, such as heat resistance, wear resistance, oxidation resistance and corrosion resistance. Aluminizing, chromizing, boronizing, siliconizing, etc. are commonly used in production. Popularly speaking, it is a chemical heat treatment process in which one or more metal atoms are infiltrated into the surface of a metal workpiece. The metal workpiece is placed in an infiltrant containing infiltrated metal elements, heated to a certain temperature, and after maintaining an appropriate time, the active atoms infiltrated into the metal element generated by the thermal decomposition of the infiltrating agent are adsorbed to the surface of the workpiece and diffused into the surface layer of the workpiece. Thereby changing the chemical composition, structure and properties of the surface layer of the workpiece.
7 Multi-component osmosis A chemical heat treatment process in which two or more elements are infiltrated into the surface of a workpiece.
Http://news.chinawj.com.cn
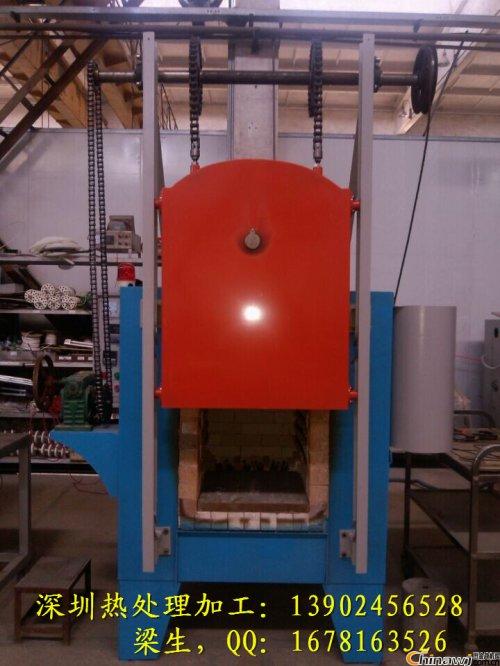
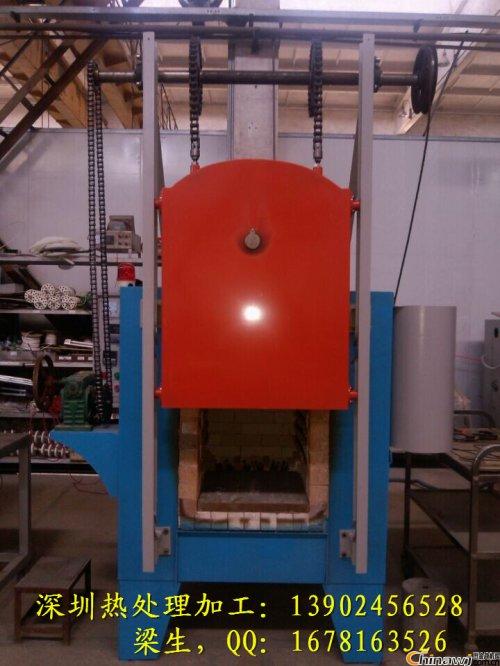
Mild Steel Pipe,Flange Plate,Carbon Steel Blind Flange,Flange Standard
YUHONG GROUP CO.,LIMITED , https://www.alloypipeline.com