With the support of the Land Rover BAR Sailing Technology Innovation Group (TIG), additive manufacturing (3D printing) technology – like many other cutting-edge technologies such as artificial intelligence, big data analytics, etc. – has been integrated into the daily work of the fleet. In this case, TIG worked hand-in-hand with Renishaw, a global measurement specialist in the production of metal additive manufacturing equipment, and on the other hand, using its more familiar plastic 3D printing technology, combined with its own advantages to prototype parts.
George Sykes, TIG project manager from PA Consulting, commented: “In the team, we apply 3D printing technology in three different levels. The simplest one is prototyping and visualization tools. When it comes to producing large quantities of customization. For parts, we can first create a full-scale prototype using 3D printing technology internally before finalizing the final product."
The Land Rover BAR Sailing Team's design room is equipped with a 3D printer, and with just a few mouse clicks, engineers can use plastic to create virtually any model that the designer conceived.
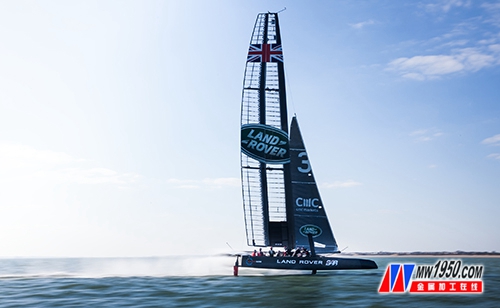
Land Rover BAR Sailing Team T3 training boat sails on the Solent Strait (Photo copyright: Harry KH Land Rover BAR Sailing Team)
“This method of prototyping is very helpful for us to develop some new parts,†said Andy Claughton, CTO of the Land Rover BAR Sailing Team. “We can actually touch the prototypes of these parts, install them on sailboats, or with the system. The other components in the connection are connected, which allows us to identify potential problems, improve the design, and ultimately put into finished product production."
The fleet has a fully equipped traditional processing workshop and a composite materials research team. With these resources, the fleet can make almost all the parts you want, but if you can use 3D printing technology to make finished parts, they will no doubt choose 3D printing. A big advantage of this approach is that it can significantly reduce costs.
The end cap of the bow is a good example. Its shape is complex and designed to reduce air resistance. The part is ideal for plastic 3D printing because there is no load on the part and only one such part is required on a sailboat. For a long time in the past, this custom end cap part has been made of carbon fiber material, but its production process is time consuming and requires a lot of experience, so the cost of parts is high. Now, once a new end cap model is designed, the fleet can produce it in a matter of hours and costs only a few pounds.
“But our top-level 3D printing application is Renishaw's metal additive manufacturing technology,†adds Sykes. “Customized parts made from metal are at the forefront of 3D printing technology.â€
Metal 3D printing manufactures parts from thin paper-like layers of fine metal powder, each of which is typically only 0.05 mm thick, and these metal powders are similar in consistency to corn starch. The additive manufacturing system operates in an inert atmosphere filled with argon—this is like the environment in a bulb; the system heats the metal powder to melt it without burning it or reacting with oxygen or impurities in the air. The laser beam is used for heating, and the laser beam is guided by a software-controlled optical lens to collect heat to precisely melt the desired processing area.
Renishaw's new generation RenAM 500M industrial additive manufacturing machine
The first part of the Land Rover BAR Sailing Team that was made with this technology was a custom-made pulley housing for the pulleys in the movable sling. The part is required to carry a high compressive load and has good wear resistance, so metal is the ideal choice. The density of all high-strength metals (weight per unit volume) is larger than that of carbon fibers, so in order to reduce weight, the parts end up with a hollow design. In addition to additive manufacturing techniques, it is difficult to manufacture such parts by any other method.
“Additive manufacturing technology has incredible potential for parts weight reduction and efficiency,†explains Andy Claughton. “For example, we spent a lot of time on hydraulic systems. Before the advent of 3D printing, the system’s All parts are manufactured by cutting solid metal blanks. The shape of the parts machined by the cutting method is very limited, which limits the freedom of design and limits the performance of the parts.
“For example, hydraulic fluids don’t like flowing through sharp corners. If they are designed this way, there will be a loss of energy. If traditional manufacturing techniques are used, this may be the only way to design a part, but with After the additive manufacturing technology, parts with smooth rounded corners can be machined, which greatly improves the efficiency of fluid transfer.
“In addition to improving the performance of the parts, we can now also make more lightweight parts, because we only need to add materials where necessary. In the past, with the use of lathes or other cutting machines, there are many restrictions on the geometry of the parts we can machine, which means We may not be able to remove some unnecessary materials, and our sailboats have to sail with these extra weights. These will not be a problem in the future."
Renishaw has produced several key parts for its hydraulic system, but the fleet is reluctant to disclose too much design detail. The new AM manifold design is said to have lost 60% in weight and more than 20% in efficiency.
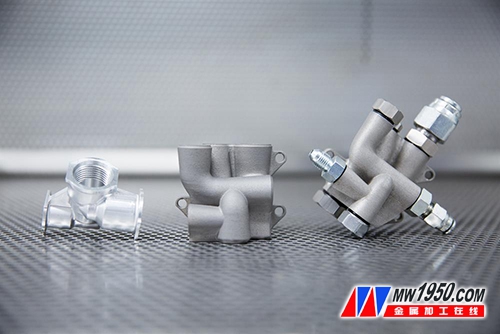
Renishaw's metal 3D printing hydraulic system parts for the Land Rover BAR Sailing Team
David Ewing, Product Marketing Engineer at Renishaw's Additive Manufacturing Products Division, said: "The partnership with Land Rover BAR helps to improve our additive manufacturing technology. Additive manufacturing encompasses a complete range of complex manufacturing solutions, from part design to process. Expertise in all aspects of the process. The best application is to use the least amount of materials to meet the design requirements, the product has practical functional advantages, and the manufacturing method should be taken into account at the time of design. We produce hydraulic for Land Rover BAR System parts are a perfect example."
“Renishaw is at the forefront of this competition for the future of manufacturing. They use their strengths to provide us with real help. This technology will take root in our manufacturing philosophy and it will be in the future. The manufacturing process is playing an increasingly important role," concludes Andy Claughton.
For more information on Renishaw's metal additive manufacturing technology, please visit
For more information on the Land Rover BAR Technology Innovation Group, please visit
Http://land-rover-bar.americascup.com/en/technical-innovation-group.html
Holiday Light
Holiday Light,Led Christmas Lights,Led Festival Light,Festival Decoration Lights
Guangdong Smart Street Lighting Co., Ltd , https://www.fldlight.com