Our company has signed a batch of concave roller supply contracts with a company. The surface quenching hardness requirement is ≥65HRC, and the quenching layer depth is 20~25mm.
According to the experience of the previous heat treatment process, the hardness requirements of the test cannot be achieved. The roll cover material is 70Cr3NiMo, and the specifications are shown in Figure 1. It is required to quench the surface of the roll cover and require quenching and tempering (hardness of 286~321HBW) before quenching.
1. Quenching process selection
For materials, in order to obtain the best performance of the material and meet its subsequent service conditions, a reasonable heat treatment method must be selected to obtain the desired structure and appropriate hardness to meet the requirements of use. Considering the special structure of the curved roller and the high hardness requirements, we choose induction hardening.
2. The structure of the workpiece leads to problems in the process
Due to the special structure of the concave roller during the heating process, the curvature changes greatly, and the heating is uneven due to the superheating effect and the angular effect of the induction heating. The small concave diameter and the sensor gap are too large, and the magnetic flux leakage is quite serious compared with other parts, and it is difficult to heat effectively. If the temperature is insufficient and the heating layer is shallow, the depth of the hardened layer is insufficient, the hardness is insufficient, and the hardness of the curved surface is not uniform. Where the diameter is large, especially at the rounded corners of the two sides, it is easy to cause the tissue to overheat or the hardened layer is too deep, resulting in excessive tissue stress and falling angle.
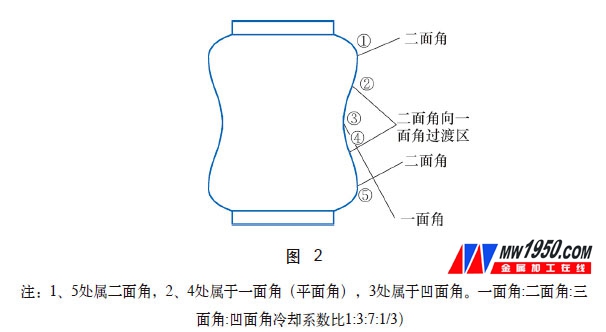
During the cooling process, the cooling coefficient is different due to the curvature of the surface of the workpiece surface, and the change of the gap causes the angle between the water line and the workpiece surface to change continuously (see Figure 2), resulting in a large hardness unevenness on the workpiece bus after quenching.
3. Quenching plan is determined
Metallographic structure and hardness non-uniformity of workpiece heat treatment can not be avoided. Various safeguard measures can only reduce the range of variation within the required range. Theoretically, at the appropriate frequency, the induction quenching heating temperature and cooling rate are more uniform and match. The more the surface hardening hardness, the uniformity of hardness and the effective depth of the hardened layer can be improved.
(1) Sensor design The sensor is an important factor affecting the electrical efficiency and heating quality. According to the traditional process specification (see Table 1 for the table quenching process standard), considering the instantaneous heating of the induction, 16mm×17mm is adopted. The square copper tube (600mm high); reduces the distance between the inductors in the small diameter, increases the current density, improves the heating efficiency, and reduces the quenching heating unevenness. The maximum diameter of the workpiece is 860mm, the minimum diameter is 730mm, and the unilateral phase difference is 65mm. Therefore, the inner diameter is 900mm, the middle is 880mm, and the inner diameter is tapered.
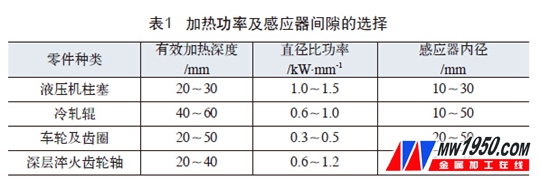
(2) Equipment selection Because the pattern requires the depth of the hardened layer to be 20~25mm, in order to achieve the layer depth, the vertical medium frequency variable frequency quenching machine is used. Because the number of inductors is large, the transformer needs to be removed (the workpiece is mounted on the induction). In the middle of the device, similar to a step-down transformer). Its frequency ≤1000Hz, not only the deeper heating depth (about 45mm), but also can form a gentle harden layer gradient, which is prepared for its use conditions, avoiding spalling and faults due to excessive hardness gradient during subsequent use. Serious failures such as falling blocks.
(3) Shift speed selection In theory, in order to achieve smooth quenching, it is necessary to reduce the cooling imbalance caused by this structure. When quenching and cooling is required in the field operation, the moving speed is increased at 1, 5; Speed ​​(see Figure 2).
(4) When the power regulating parts are quenched, if the temperature is too high, the local grains will be coarse, which will deteriorate the structure; if the temperature is too low, the hardness will not meet the requirements. Therefore, the temperature in the required hardened zone (depth direction) should be kept within the specified range. We choose to simultaneously heat to the temperature, and then continuously spray quenching. The minimum section diameter of the workpiece quenching zone is 730mm, and the gap between the inductor and the workpiece is 75mm. In order to effectively heat up, to meet the quenching temperature requirements, the heating should be continuously increased during the heating process from one end to a small intermediate part (ie from 5 to 3). When heating to interval 2, start to reduce power.
(5) Final quenching heating method The larger the gap between the inductor and the workpiece, the lower the electrical efficiency, and the same hardened layer depth value can be realized with different current densities and different heating times. In order to make the workpiece heating temperature uniform, it is continuously spray-quenched by means of transforming power and shifting speed. In order to prevent the heating temperature from being low, in the continuous spray cooling, the power and the moving speed continuously change with the curved surface, so that the temperature and the cooling speed are matched with the surface of the workpiece, so that the hardness layer is deep and uniform.
4. Process plan implementation
Before the actual workpiece surface quenching, the unilateral margin of the surface is 1.5mm, the surface roughness Ra=3.2μm, and the previous quenching hardness is 308~325HBW, which satisfies the surface induction quenching condition. 25 mm is the minimum hardened layer depth, while the quenching cooling water pressure is 2.3 MPa. The specific data of the quenching heating process is shown in Figure 3.
5. Hardness testing and analysis after quenching
After cooling for 50 minutes, the roll surface temperature is 32-35 ° C, and the roll body hardness is detected as follows:
Busbar 1: 67HRC, 66HRC, 65HRC, 67HRC; busbar 2: 67HRC, 65HRC, 66HRC, 66.5HRC.
After 180 ° C × 30 h tempering, after cooling, the hardness is basically satisfied, the hardness fluctuation is within the required range, and accumulated valuable experience for induction hardening of the workpiece with large curved surface.
About the author: Ma Xinnian, Ge Huarong, Peng Yuanfei, Yuan Xiaoting, Shaanxi Fuping Zhongye Shaanxi Rolling Equipment Co., Ltd., heat treatment workshop.
FEATURES:
Light weight; good elasticity, weather resistance; long serving life.
PRESSURE REQUIRED:
I.D.
(inch/mm)
|
Working Pressure
(Bar / Mpa / Psi)
|
Bursting Pressure
(Bar / Mpa / Psi)
|
1``
|
25
|
13 upto 25
|
1.3 upto 2.5
|
190upto365
|
39upto75
|
3.9upto7.5
|
570 upto1090
|
1-1/4``
|
32
|
8 upto 25
|
0.8 upto 2.5
|
120upto365
|
24upto75
|
2.4upto7.5
|
350 upto1090
|
1-1/2``
|
38
|
8 upto 25
|
0.8 upto 2.5
|
120upto365
|
24upto75
|
2.4upto7.5
|
350 upto1090
|
1-3/4``
|
45
|
8 upto 25
|
0.8 upto 2.5
|
120upto365
|
24upto75
|
2.4upto7.5
|
350 upto1090
|
2``
|
52
|
8 upto 25
|
0.8 upto 2.5
|
120upto365
|
24upto75
|
2.4upto7.5
|
350 upto1090
|
2-1/2``
|
64
|
8 upto 25
|
0.8 upto 2.5
|
120upto365
|
24upto75
|
2.4upto7.5
|
350 upto1090
|
2-3/4`
|
70
|
8 upto 25
|
0.8 upto 2.5
|
120upto365
|
24upto75
|
2.4upto7.5
|
350 upto1090
|
3``
|
75
|
8 upto 25
|
0.8 upto 2.5
|
120upto365
|
24upto75
|
2.4upto7.5
|
350 upto1090
|
4``
|
102
|
8 upto 16
|
0.8 upto 1.6
|
120upto235
|
24upto48
|
2.4upto7.5
|
350 upto700
|
5``
|
127
|
8 upto 13
|
0.8 upto 1.3
|
120upto190
|
24upto39
|
2.4upto3.9
|
350 upto570
|
6``
|
152
|
8 upto 13
|
0.8 upto 1.3
|
120upto190
|
24upto39
|
2.4upto3.9
|
350 upto570
|
APPLICATIONS:
Fire-fighting; Shipping; petroleum; Chemical industry; Agriculture; Mining
Color available:white;red;yellow; or as per customer`s instruction
STANDARD:GB6246,EN14540,UNI9487; or as per customer`s instruction
STANDARD LENGTH:10M up to 40M
Synthetic Fire Hose
Synthetic Fire Hose,2`` Fire Hose,Synthetic Rubber Fire Hose,Fire Hose For Fire Cabinet
NANTONG SENTIAN FIRE-FIGHTING EQUIPMENT CO.,LTD. , http://www.firehosefactory.com